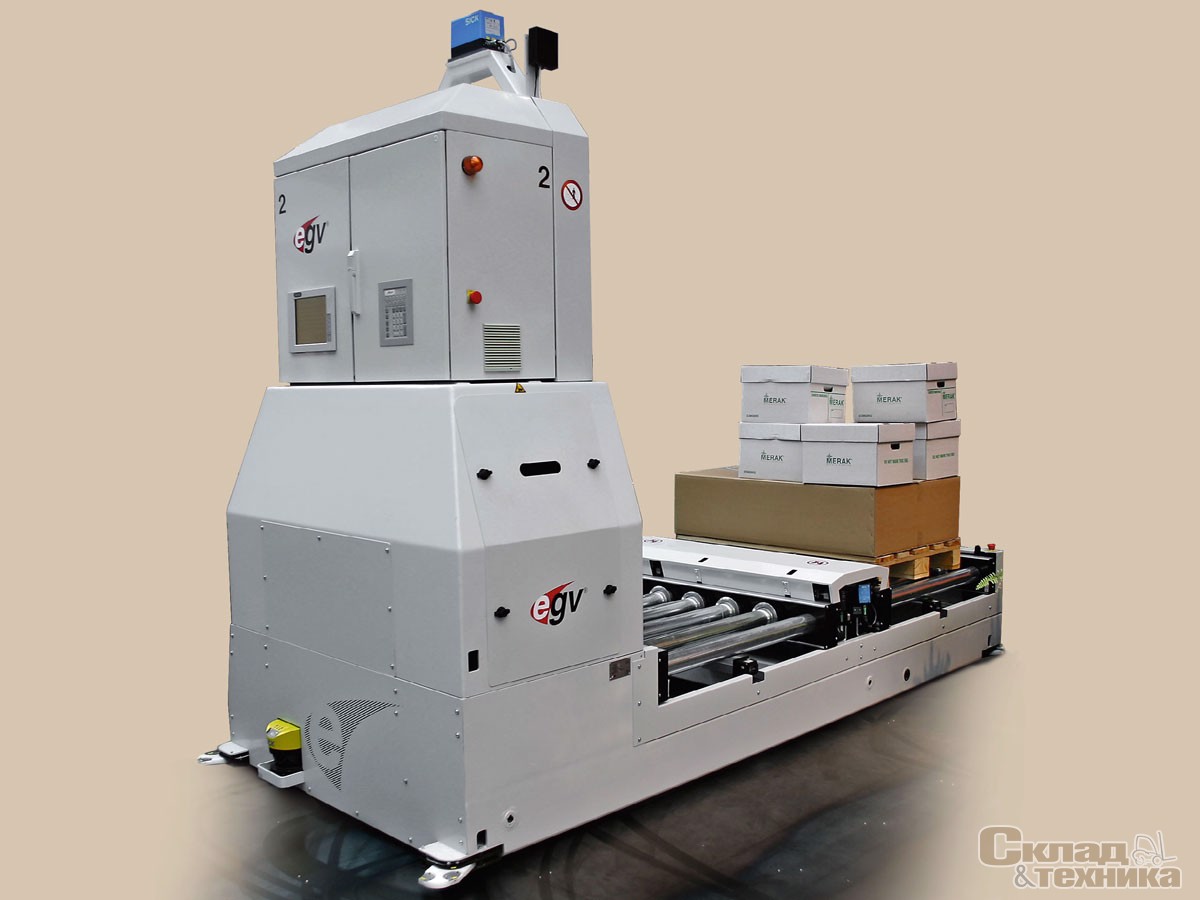
Автоматизированные транспортные системы
Пример истории автоматизированных транспортных систем (АТС), работающих без водителя, показывает, какие неожиданные повороты бывают порой в развитии нового вида техники. После почти молниеносного проникновения АТС во многие отрасли промышленности и очень больших ожиданий от их использования последовал период «охлаждения», а затем и почти полного их забвения. Сегодня изготовители АТС видят свою задачу прежде всего в том, чтобы вернуть доверие потребителей этой продукции, учитывая ее технические и экономические преимущества, в частности многочисленные инновации, использованные в новых разработках, которые позволяют значительно повысить производительность АТС.
В России в силу неразвитости производства как напольного транспорта, так и полностью автоматизированных систем транспортировки грузов устоявшаяся терминология по этой технике отсутствует, поэтому мы взяли на себя смелость ввести такое понятие, как АТС. За рубежом для обозначения подобных систем общепринятыми являются аббревиатуры AGVs (от англ. Automatic Guided Vehicle Systems) и FTS (от нем. Fahrerlose Transportsysteme). – Прим. ред.
Когда автоматизированная транспортная техника становится АТС?
Автоматизированные транспортные системы, рассматриваемые в настоящей статье, следует отличать от иных автоматизированных транспортных устройств: они работают без участия операторов, предназначены для «внутрипроизводственного» употребления и разрабатываются на базе ведомых средств напольного транспорта, основной задачей которого является перевозка материалов, но не людей. АТС используют как внутри зданий, так и снаружи, а состоят они из многочисленных функциональных групп: одной или многих единиц работающего без водителя транспортного оборудования (робокаров), навигационного управления, устройств определения местонахождения и положения, устройств передачи информации, а также инфраструктуры и периферийных устройств (согласно VDI 2510 «Fahrerlose Transportsysteme (FTS)» Berlin: Beuth-Verlag 2005). (Такое автоматизированное транспортное оборудование существует во многих вариантах исполнения.) При этом общая производительность и надежность АТС определяется свойствами отдельных систем-компонентов и успешностью их интеграции: какие-либо серьезные усовершенствования достижимы только при комплексном синхронном внедрении нескольких инноваций в единую систему.
![[b]Функциональные группы АТС[/b]](/article/10543-kamo-gryadeshi-ats/Images/10.jpg)
От эйфории к реализму
Первые АТС появились в ФРГ в начале 1960-x годов, и уже в 1970-е и 1980-е страну охватил внедренческий бум. Инициатором его стала в первую очередь всегда ориентированная на автоматизацию автомобильная промышленность: почти все немецкие автомобилестроители сделали ставку на прогрессивную и, как тогда казалось, гибкую технологию. Первооткрыватели новых устройств на этой стадии смогли реализовать системы, включившие в себя в общей сложности около 500 единиц транспортного оборудования. Такой успех стимулировал развитие АТС, и в ФРГ в кратчайшие сроки появилось много новых изготовителей. В этой «АТС-эйфории» из-за возрастающей конкуренции и частично вследствие недостаточного опыта компаний наряду с абсолютным ростом числа реализованных систем, к сожалению, значительно возросло и количество не слишком удачных примеров использования, что вызвало резкую критику со стороны эксплуатационников. Важным фактором, определившим негативное отношение к новинкам, стала деятельность некоторых изготовителей, которые буквально любой ценой хотели проникнуть на перспективный рынок и при этом автоматизировать производства, которые при существующем на тот период уровне АТС и их компонентов не могли работать достаточно надежно и/или экономично. Вместе с большим числом систем, которые работали надежно, но не пользовались вниманием средств массовой информации, с конца 1980-х годов увеличилось число сообщений о практических случаях использования, когда АТС не оправдали себя с точки зрения логистики, гибкости и экономичности. Основными причинами спада интереса к АТС в Германии, как было отмечено на Первом семинаре по АТС (Дуйсбург, 1991 г.), стали следующие:
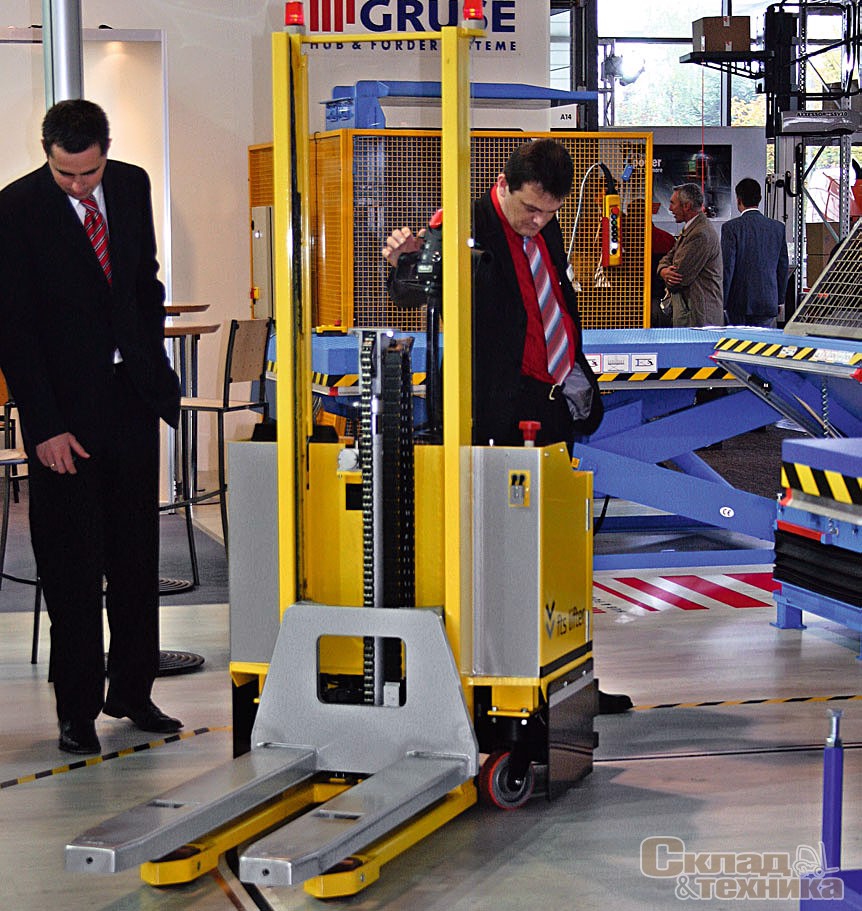
- недостаточная непрерывная логистическая производительность: частые отказы оборудования по причине ненадежности датчиков, управления и навигационных систем, вмонтированных в пол; очень низкая скорость движения и слишком продолжительное время обработки груза; излишнее удлинение трассы из-за особенностей существующей навигационной системы;
- недостаточная гибкость оборудования: движение по индуктивному проводнику, что вынуждает оборудование перемещаться только по постоянной трассе; система управления, которая настроена на конкретные навигационные устройства, встроенные в пол, в результате чего оборудование разных изготовителей не может совместно работать в одной системе автоматизации;
- недостаточная экономичность: изготовители АТС в большинстве случаев выпускали оборудование громоздкое, тяжелое и дорогое; новые технологии, например устройства управления, индуктивная техника и датчики, были достаточно сложными, из-за чего текущие производственные расходы значительно возрастали.
В результате к началу 1990-х годов рынок АТС сильно сократился. Одной из первых от новых технологий отказалась автомобильная промышленность. Негативное отношение к АТС росло как снежный ком. Положение усугубилось тем, что из-за отсутствия заказов известные изготовители не смогли выдержать ценовой конкуренции с обычным оборудованием, а расходы потребителей на обеспечение последующей эксплуатации АТС увеличились. Как следствие, доверие потенциальных потребителей к этим устройствам было основательно подорвано, и в последующий период «АТС-рецессии» их не внедряли даже тогда, когда экономическая эффективность была очевидна. Чтобы изменить положение и дать толчок дальнейшему развитию перспективной технологии, в первую очередь требовалось критически проанализировать причины снижения привлекательности АТС, что позволило бы сделать выводы об их возможностях.
Типы АТС
АТС довольно разнообразны по конструкции, поскольку их создают для конкретных условий эксплуатации. Правильно оценить эффективность их применения на том или ином предприятии не специалисту сложно, для этого надо хорошо ориентироваться в возможностях АТС. В целом можно выделить следующие основные виды этих устройств.
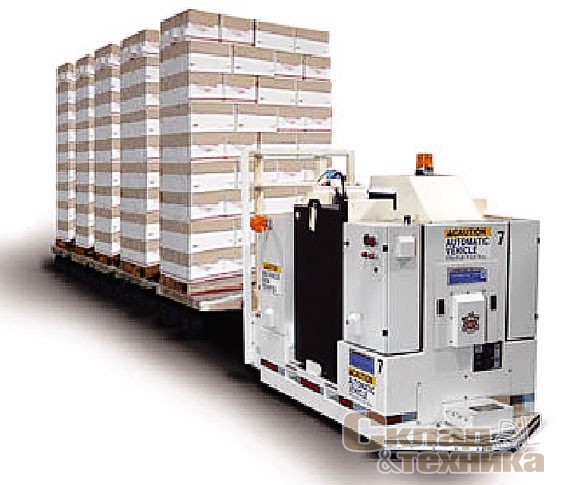
Автоматизированный тягач стал первым транспортным средством, на котором применили автоматическое управление, и до настоящего момента остается едва ли не самым популярным типом АТС. Буксировщик может тянуть одну или много тележек или прицепов с грузом общей массой от 3,5 до 30 т, причем не только внутри склада, но и для доставки продукции из производственных цехов на склад и обратно, снабжения сборочных линий автомобилестроительных предприятий. Системы поездов вообще применяют там, где изделия необходимо перемещать грузы на большое расстояние, в том числе между зданиями под открытым небом. Поскольку каждый поезд может перемещать до 16 поддонов в строго установленные сроки и к заданным точкам разгрузки, такой способ быстро окупает себя и более предпочтителен по сравнению с вилочными погрузчиками или тягачами, управляемыми людьми.
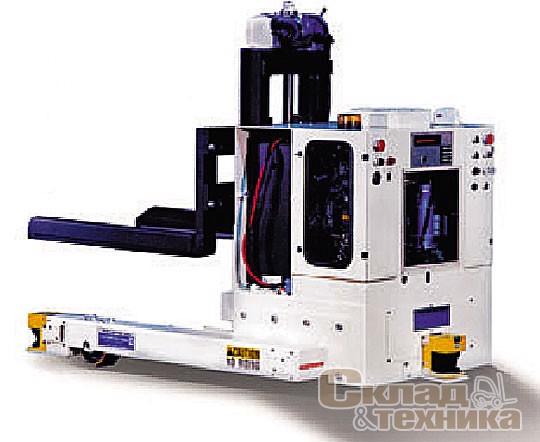
Автоматические тележки (штабелеры) для перевозки поддонов применяют для выполнения функций распределения и выполняют их на базе традиционного оборудования. Они могут работать в двух режимах – автоматическом и ручном, т. е. управляться оператором, как обычные ведомые средства напольного транспорта. В автоматическом режиме тележка с грузом сама идет по проложенной трассе к определенному месту хранения, после чего опускает вилы, снимает поддон и автоматически перемещается порожней к новому месту загрузки.
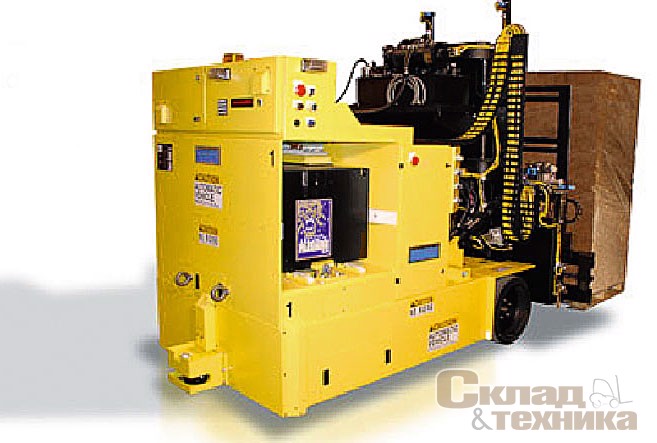
Автоматизированный погрузчик обслуживает грузы как на уровне пола или конвейера, так и на стеллажах, а в некоторых случаях может сложить грузы в штабель. Применение АТС для автоматизации работы погрузчика – дело относительно новое. Так как эти транспортные средства – одни из самых дорогих типов AТC, их использование оправдано только там, где нужна полная автоматизация погрузочно-разгрузочных работ. Чтобы автоматизированные системы для погрузчиков эффективно обслуживали склад, требуется прокладка большего количества сложных навигационных трасс с множеством пересечений и точное позиционирование грузов на полу или стеллажах. Это обычно требует от системы управления большей сложности и точности, чем в случаях других АТС, зато они выгодно отличаются большей гибкостью при необходимости объединения в общую структуру вместе с другими подсистемами.
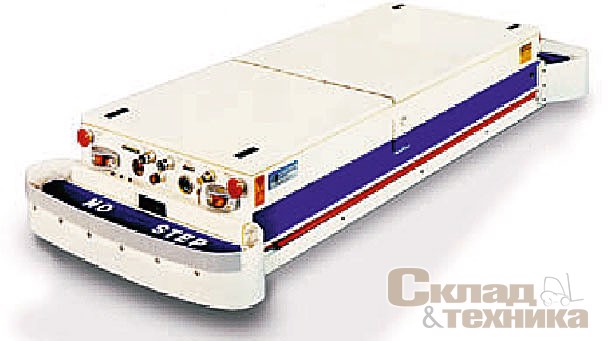
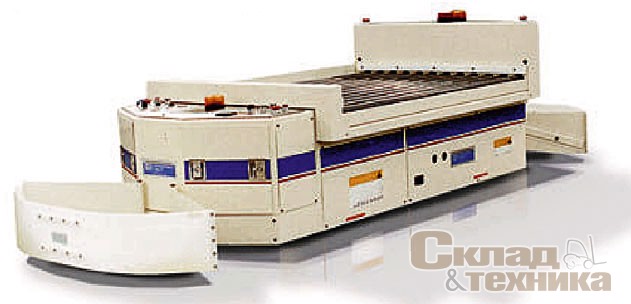
АТС для перевозки штучных грузов обычно применяют для транспортировки грузов, которые постоянно двигаются по индивидуальным трассам. Как правило, они не только сами транспортируют груз, но и оборудованы площадками с вращающимися роликами или цепями, по которым груз может автоматически перемещаться. Площадки помимо этого могут иметь функции подъема-опускания. Обычно такие системы весьма популярны там, где требуется объединить конвейер с другими технологическими этапами производственного процесса или системами хранения. Эти АТС широко применяют для горизонтальной транспортировки объемных грузов на средние расстояния между другими автоматизированными подъемно-транспортными подсистемами, объединенными в единый комплекс.
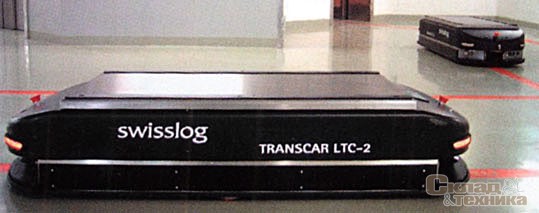
АТС для перевозки легких грузов чаще всего применяют для доставки компонентов из мест компактного хранения к индивидуальным автоматизированным рабочим местам, где операторы осуществляют сборку. Такое оборудование транспортирует грузы массой до 150 кг, например, на подносах или в пластиковых контейнерах, и размеры его небольшие, причем настолько, что оно может идеально маневрировать в помещениях с узкими проездами. Такие АТС эффективны для применения на предприятиях по выпуску электронных изделий, на небольших сборочных производствах – везде, где есть нехватка рабочих площадей в помещениях.
Автоматические транспортные средства для обслуживания сборочных линий – это своего рода адаптация АТС для перевозки легких грузов к технологическим процессам, состоящим из нескольких последовательных этапов сборки изделий. Такие системы только начинают применять в США. Например, управляемые транспортные средства последовательно транспортируют с одного рабочего места на другое главные элементы изделия – корпуса двигателей, коробок передач либо шасси, к которым в процессе сборки добавляют другие компоненты. Другие компоненты помещены на подносы, которые перемещаются вместе с основным изделием на транспортном средстве. Когда процесс сборки закончен, готовое изделие снимается, а транспортное средство отправляется к начальному этапу сборки. Применение таких систем придает производственному процессу высокую гибкость, позволяя параллельно вести процессы, а также позволяет отслеживать этапы сборки и учитывать временные нормативы на разных ее стадиях. Обычно эти системы объединены в полную систему производства, которая требует компьютерного контроля и управления и точного планирования.
Существуют и другие виды АТС, например, для перевозки грузовых контейнеров на открытых терминальных площадках портов. В последнее время несколько компаний предложили тележки-шаттлы для транспортировки паллет на стеллажах типа «drive-in».
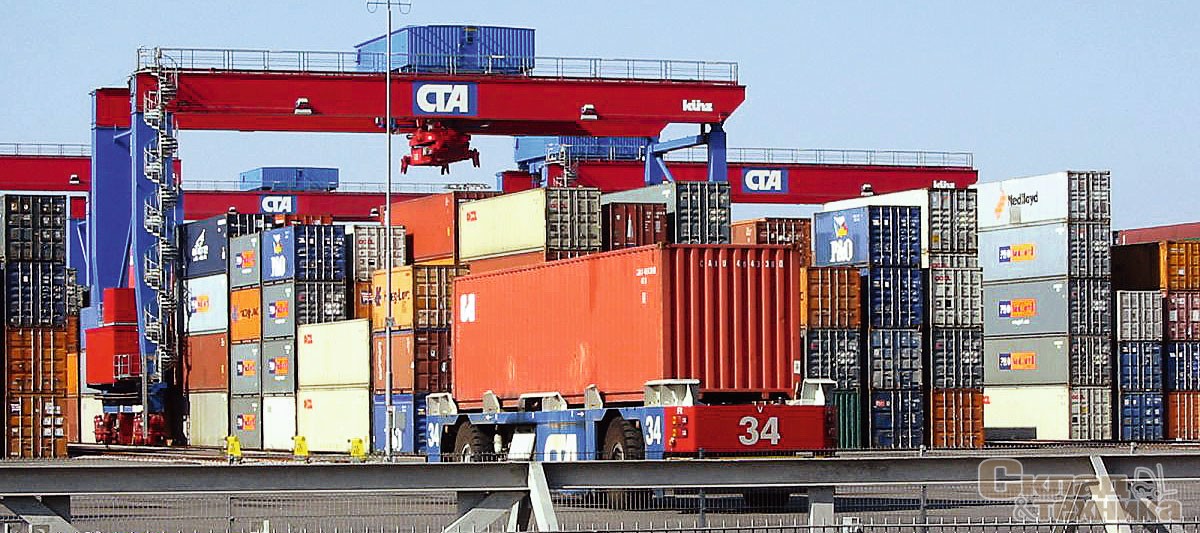
В поисках диалога
Наиболее подходящей площадкой для решения вопросов развития АТС стала созданная еще в 1986 г. при Союзе немецких инженеров (VDI) секция В7 «Fahrerlose Transportsysteme (FTS)» («Работающие без водителей транспортные системы»), которая представляет собой независимый форум изготовителей самих систем и их компонентов, производственников, исполнителей, а также исследовательских учреждений. Секция В7 поставила перед собой задачу поддержать эксплуатационников соответствующими близкими к практике нормативами, а также в рамках своих возможностей проводить работу по популяризации на регулярных семинарах по проблематике АТС. В ходе постоянного диалога производственных компаний, исследовательских учреждений и изготовителей были уточнены и конкретизированы требования к АТС, в результате чего их смогли представить как серьезно воспринимаемую системную альтернативу существующим технологиям во многих областях промышленности.
В рамках диалога изготовители смогли доказать, что АТС надежно функционируют, их новые компоненты (например, в сфере навигации и передачи информации по радио) освоены, а требуемая безопасность персонала и оборудования при эксплуатации наконец достигнута. Пользователи и производственники сумели объединить свои требования в долговременной перспективе и с опережением, а изготовители получили повышенную надежность планирования. В качестве иллюстрации ниже представлены опыт, требования и технологические оценки по АТС, сделанные фирмой DaimlerChrysler AG.
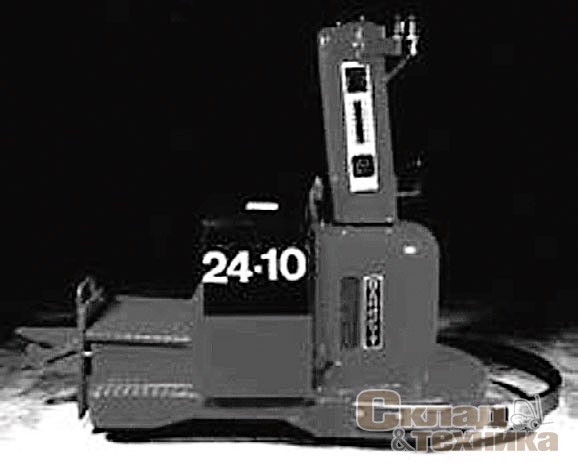
АТС в США
Первая АТС (AGV) для индустриального применения, которая представляла собой автоматическую вилочную электротележку, изобретена именно в Штатах компанией Barrett Electronics Corporation в 1954 г. Термин AGV (автоматически управляемое транспортное средство) фактически введен в 1980-х, а до этого новые устройства называли driveless vehicles (транспортными средствами). Сегодня одно из первых образцов driveless vehicles можно видеть в демонстрационном зале компании Siemens Logistics and Assembly Systems в Гранд-Рапидсе (США). Siemens L&A приобрела Barrett Electronics в 1983 г. Линия изделий Barrett AGV, развитие которой продолжено как часть программы оборудования Siemens L&A, насчитывает теперь более 13 разных типов АТС.
За прошедшие полвека в Соединенных Штатах было установлено более чем 3 тысячи АТС, куда входит от одного до более чем 100 единиц транспортных средств (робокаров). В настоящее время в стране около полудюжины основных изготовителей этого оборудования производят ежегодно приблизительно 80% всех АТС и 20% систем – примерно 12 других компаний. За последние 10 лет рынок АТС в США составлял от 40 млн. до 100 млн. USD в год, что составляет примерно 30…80 систем.
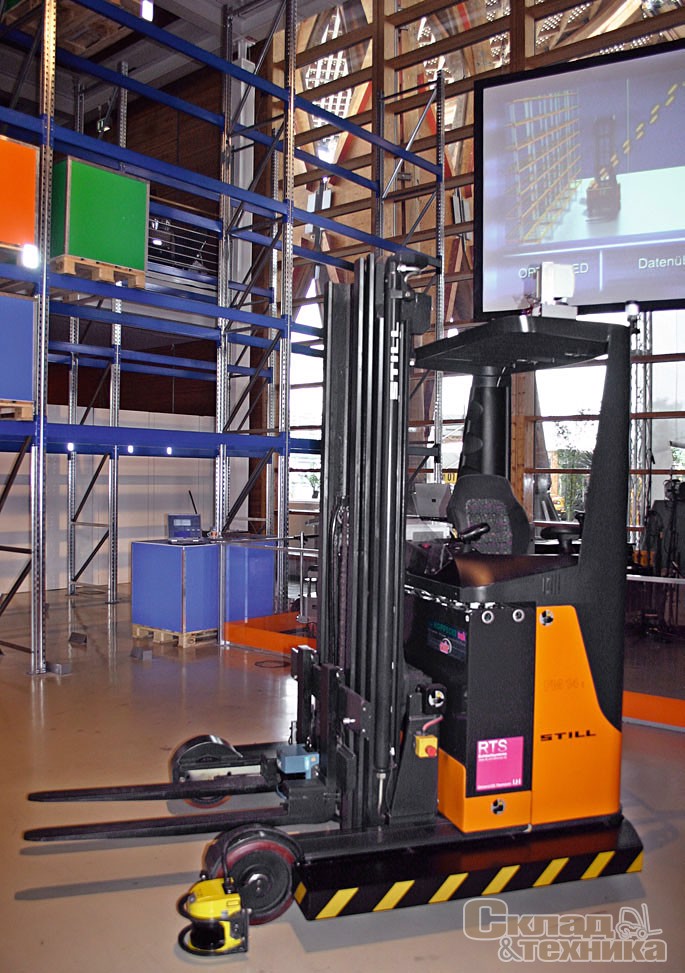
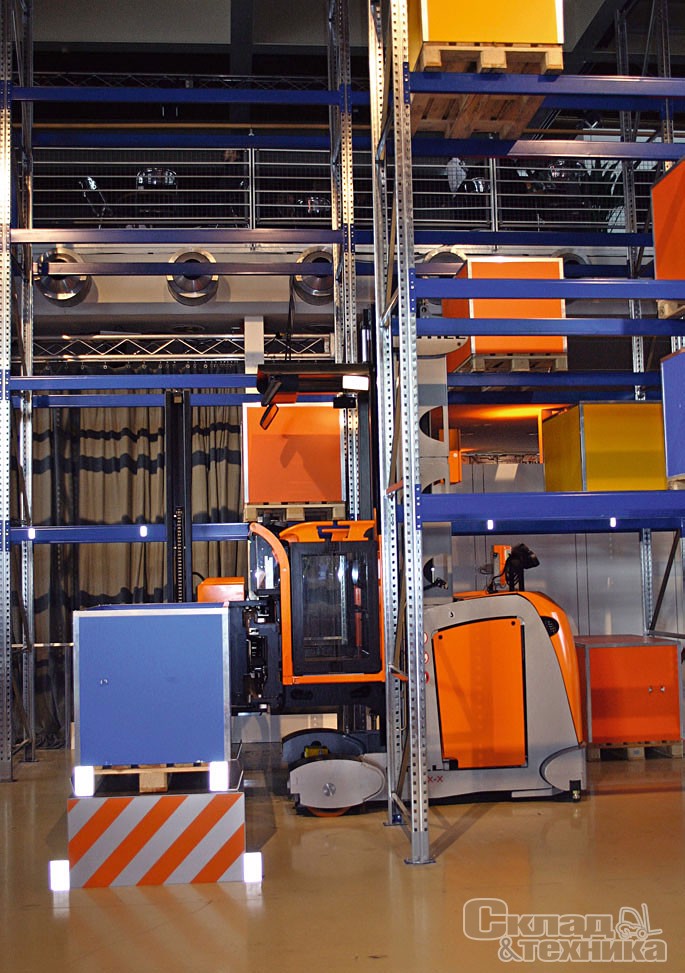
Требования с позиций эксплуатационника
Компания Mercedes-Benz, старейший немецкий изготовитель легковых автомобилей, всегда выделялась среди автомобилестроителей весьма взвешенным подходом как к традициям, так и к инновациям. Этот признак характеризует не только качественные и технически амбициозные изделия фирмы, но и технологические производственные системы, за создание которых внутри DaimlerChrysler отвечает Mercedes Car Group (МСG). Концепция, созданная DaimlerChrysler и Mercedes Car Group (МСG), и конкретные средства транспортировки объединены в технологической системе Mercedes-Produtionssystem (MPS), берущейся за основу при планировании, а также в ходе постоянных улучшений в технологической цепочке.
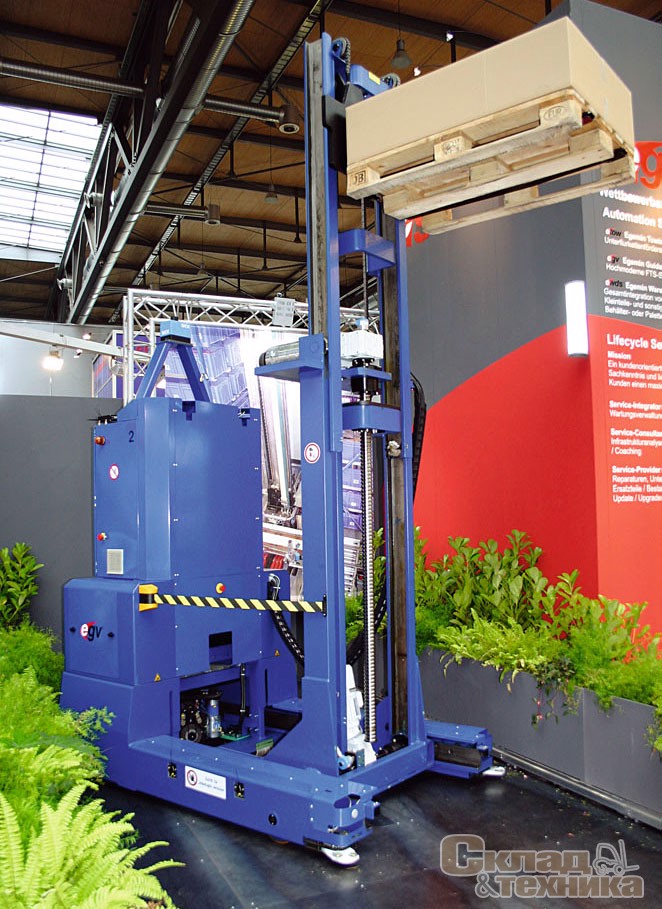
Значение логистики и организации материальных грузопотоков в ориентированной на сквозное движение системе МРS заметно выше, чем в других производствах, а потому для стратегической поддержки и координации классического оперативного планирования, которое применялось на всех участках производства, были организованы секторы центрального фабричного и производственного планирования. В этих секторах совместно с собственным исследовательским подразделением концерна и разработкой продукции были созданы решения по логистике и транспортной технике. Центральной задачей каждого ориентированного на успех производственного предприятия наряду с собственной творческой деятельностью является своевременное ознакомление и систематическая оценка новых производственных и логистических технологий, пригодных для организации собственных процессов. Это касается не только новых концепций, но и постоянного мониторинга известных методов в отношении прироста инноваций, которые можно экономично применить на собственном производстве.
Благодаря планируемому опережению для своевременной интеграции потенциальных инноваций в производство должны быть заранее определены и оценены эффективность и последствия применения. Тем самым мониторинг приобретает функцию «лоцмана».
Концерн DaimlerChrysler для изучения многочисленных инноваций в секторе АТС в рамках регулярно проводимых технологических мониторингов для всей транспортной техники с электропитанием постоянным током и при тесном взаимодействии c VDI, Ганноверским университетом, а также сектором логистики Технического университета Берлина провел исследование нынешнего уровня и перспектив АТС, конкретной целью которого было облегчить процессы логистического планирования на предприятии, проанализировав существующие решения для различных сценариев применения. Кроме того, такое планирование уже на самой ранней стадии должно стать проще, быстрей, экономичней и надежней благодаря разработке соответствующей систематизации АТС и ее интеграции в поддерживающий планирование блок программного обеспечения. Чтобы достичь этих целей, надо было определить, какой потенциал и в каких случаях применения есть у существующих типов АТС как для сегодняшней логистики предприятия, так и в самом ближайшем будущем.
SmartLoader™ – первый полностью автоматический вилочный погрузчик
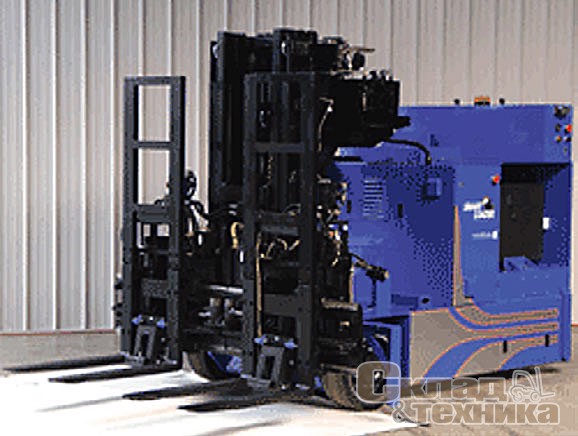
Американская компания Jervis B. Webb Company, один из лидирующих производителей погрузочного оборудования, в этом году запускает новый продукт – первый полностью автоматический вилочный погрузчик SmartLoader™, который может работать без участия человека круглосуточно 7 дней в неделю. К его разработке привлекли специалистов военно-промышленного комплекса США, применивших в конструкции модели ракетные технологии. Погрузчик ориентируется в пространстве с помощью компьютерной навигационной системы, аккуратно выдерживая траекторию движения и выполняя поставленные задачи. Свое точное местоположение погрузчик определяет по вмонтированным в пол транспондерам. SmartLoader™ интегрирован в систему управления складом, что обеспечивает контроль за его действиями в режиме реального времени. В погрузчик встроены средства, обеспечивающие безопасность, в том числе лазерный сканер, идентифицирующий препятствия на пути, контактные датчики, размещенные по периметру корпуса, оптические элементы. Заряда батарей хватает на 8 часов работы, после чего погрузчик самостоятельно становится на подзарядку.
SmartLoader™ обрабатывает пакетированные грузы разной конфигурации, перемещая их от пакетоформирующей машины или со стеллажей в любой трейлер без помощи каких-либо проводов, лазеров или магнитов. Он также может составлять штабеля и снимать предметы с конвейера. Погрузчик может брать по одной или по две паллеты одновременно, адаптирован к автомобилям разных размеров, разным углам наклона пандуса и может укладывать паллеты впритык или с зазором.
Одна из крупных продуктовых компаний уже использует более дюжины таких погрузчиков, которые работают по три смены в сутки от пяти до семи дней в неделю. Таким образом компания снизила издержки, особенно связанные с непрерывной загрузкой трейлеров, а также с простоями, обслуживанием техники и порчей товара.
Методика исследований
Главной целью при оценке технологических и конструктивных тенденций развития в сфере представленных АТС является абстрактное рассмотрение реальных уже сегодня и потенциальных областей использования. Исходя из допущения, что совокупность всех областей (на графике – полей) использования АТС ограничена, с одной стороны, технически, а с другой – экономически, она была развернута по двум осям (см. рис.). Горизонтальная ось указывает на области, начиная с тех, где в настоящее время уже возможно экономически использование АТС, и до новых полей применения, которые откроются только через повышение экономических показателей этих систем (эффективности, рентабельности и т. д.).
Еще одну границу могли бы представлять требования закона, например, на использование АТС в системе общегородского транспорта, что, однако, в данном случае осталось без внимания.
![[b]Схема для оценки новых технологий и концепций в области АТС[/b]](/article/10543-kamo-gryadeshi-ats/Images/14.jpg)
Ось разделена на три отрезка. Слева расположена область с экономически освоенными полями использования. Отрезок в середине оси маркирует область (поле), где АТС уже целесообразно использовать, но граничные условия ее применения должны быть улучшены определенной новой технологией или экономической концепцией. «Экономическая» граница символизирует переход к полям применения, в которых при существующем уровне техники внедрение пока обходится слишком дорого. На крайнем правом конце оси находится соответственно область из новых в экономическом смысле полей применения.
Вертикальная ось служит для независимой оценки технологической перспективы внедрения АТС. Внизу располагается область с полями применения АТС, уже реализованными через современные технологии и концепции, над ней – область полей применения, где через технологические или конструктивные нововведения и разработки существующие требования выполняются лучше, чем прежде. Сверху лежит участок областей применения, которые будут открыты благодаря новым технологическим решениям; он отделен от известных полей применения «технологической» границей, выше которой использование АТС по техническим причинам пока не представляется возможным.
Тенденции развития АТС были исследованы в соответствии с их функциональным делением по следующим областям:
- модульные структуры транспортного оборудования и стандартные компоненты;
- модульные системы управления;
- навигационные системы и системы безопасности;
- энергоснабжение;
- приспособленность к работе вне помещений.