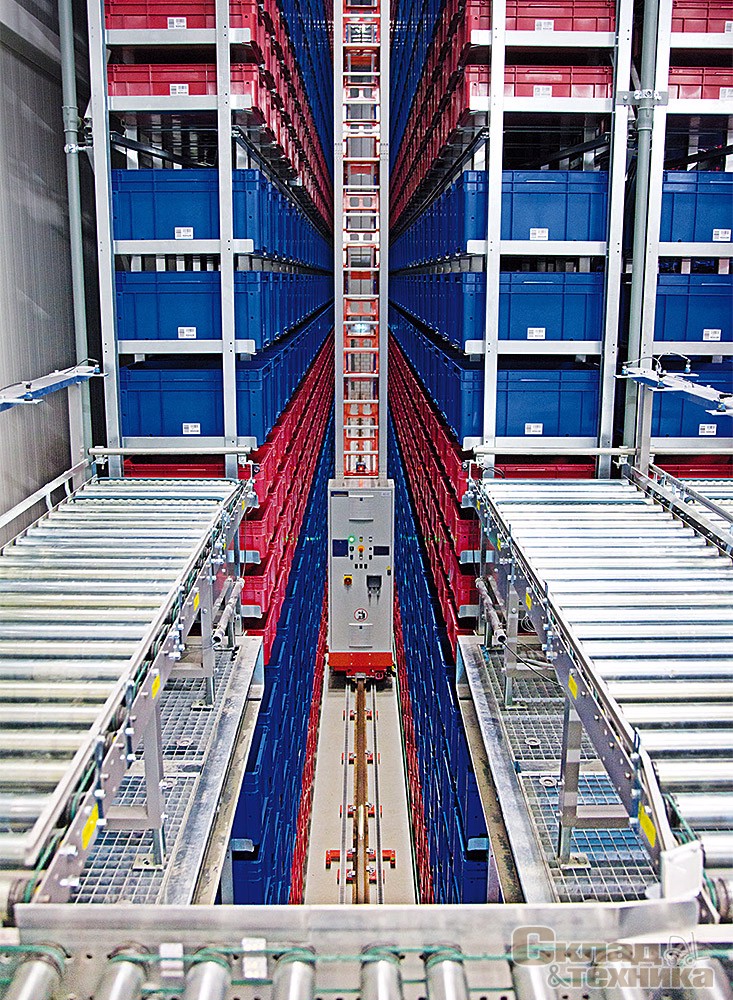
Автоматизированный высотный склад (АВС) от Stöcklin Logistik для крупнейшего предприятия Швейцарии
Новое успешное решение Stöcklin Logistik по внутренней логистике для крупнейших предприятий Швейцарии по торговле высококачественной сталью.
АО Hans Kohler, самое крупное предприятие Швейцарии по торговле высококачественной сталью, инвестировало 4,5 млн. швейцарских франков в новый склад для фитинга, расположенный в Дитиконе. Благодаря автоматизированной системе управления все процессы на предприятии теперь осуществляются гораздо эффективнее, кроме того этим была заложена надежная основа для поддержания его успешного функционирования в будущем.
Автоматизированный высотный склад (АВС), который визуально гармонично вписывается в ландшафт, является скорее исключением из общего правила. Новый склад АО Hans Kohler в Дитиконе тем более достоен внимания, что представляет собой образец гармоничного окружающей среде промышленного дизайна. Помимо этого он имеет интегрированную систему материально-технического обеспечения. После успешного ввода в эксплуатацию склада этого предприятия c главным офисом в Цюрихе в августе 2012 г. у местных предприятий среднего бизнеса появилась возможность быстрее и эффективнее обрабатывать свои заказы. Причиной этого стала автоматизация всего оборудования, которая значительно повысила бесперебойность работы, а также его эксплуатационную надежность.
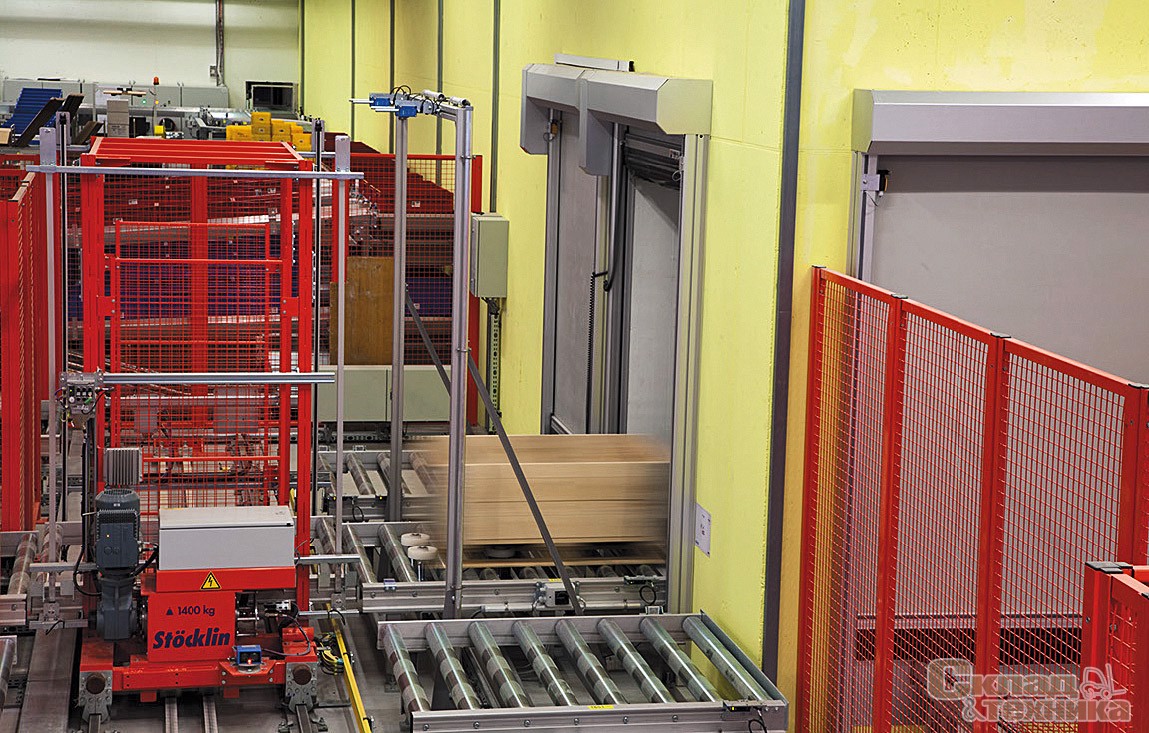
Максимальная вместительность и производительность при небольшом пространстве
Новый склад для фитинга является частью обширного проекта реорганизации. Уже в 2008 г. АО Hans Kohler начало делать первые планировки для GIZELA (Giessen Zentral Lager). Менеджер по логистике Бенно Кюндиг (Benno Kündig) так описывает исходную ситуацию: «Мы занимались тремя складами в Дитиконе и Шлирене, которые не отвечали современным требованиям. Вместимость складов была небольшой и не была ориентирована на рост оборотов в будущем». Логистическое оборудование тоже не соответствовало современным стандартам, и высокая степень автоматизации при существующих объемах хранения нецелесообразна. Задача заключалась в том, чтобы построить на уже имеющемся, относительно небольшом земельном участке новое, максимально эффективно использующее площадь и оптимально оборудованное предприятие для хранения, комплектации и оборота примерно 7,5 тыс. изделий, разделенных приблизительно на 25 тыс. различных партий. В итоге было построено здание площадью 8 тыс. м2 со встроенным автоматизированным высотным складом (АВС) для палет, имеющих три различных высоты, и автоматизированным складом мелкого товара (АСМТ). На нижнем этаже сразу же был оборудован отдел комплектации заказов площадью 1,2 тыс. м2 и с четырьмя рабочими местами. Такая же площадь на верхнем этаже, которая при необходимости может быть использована в дальнейшем, была подготовлена для обработки грузов с помощью подъемно-транспортной техники. «Благодаря целенаправленному расчету параметров здания и вмонтированной технике мы использовали имеющуюся площадь полностью и в равной мере оптимально», – объясняет Кюндиг. Учтена и перспектива развития бизнеса в дальнейшем: с этой целью АСМТ был как бы подвешен сбоку, тем самым оставив восточной части здания возможность для дальнейшего расширения.
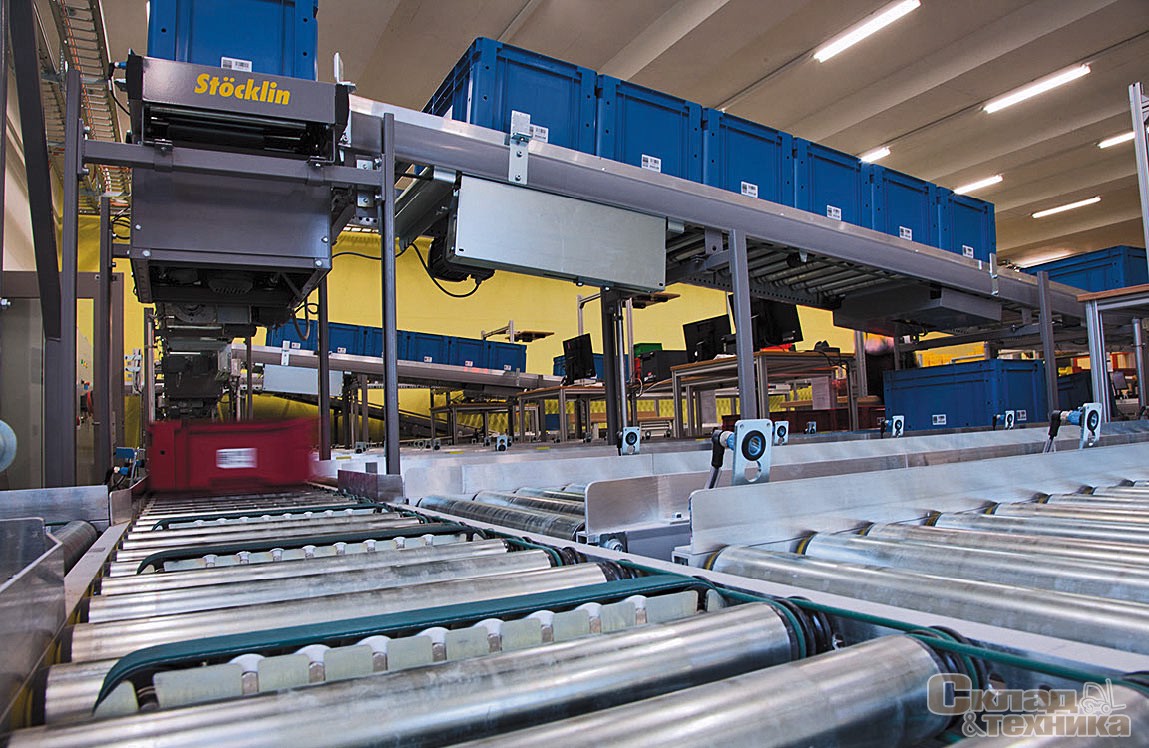
Все оборудование из одних рук
В конце июня 2011 г. АО Stöcklin Logistik была поручена реализация подходящего концепта складов для фитинга. Ее концепция и специфика были нацелены не только на организацию АВС и АСМТ. В большей степени при последующих работах АО Hans Kohler полагалось на швейцарских специалистов по внутренней логистике, которыми были разработаны стеллаж для хранения пластиковых контейнеров, автоматизированный склад пластиковых контейнеров для АСМТ, управление с использованием программируемых логических контроллеров и калькулятор материалопотока, включая визуализацию аппаратуры, противопожарные ворота.
Кроме того, коммерческое предприятие одновременно заказало у генерального подрядчика и системного интегратора большое количество различной напольной техники с надписями «made by Stöcklin», которое сегодня осуществляет самые разнообразные задания по транспортировке и манипуляциям с грузами. «Общеизвестно, что Stöcklin означает качество и инновации», – утверждает Ханс Кохлер (Hans Kohler), исполнительный директор и член совета директоров. Решающее значение в выборе заказчика имел гарантированный Stöcklin Logistik срок службы изделий в 10 лет. Руководитель проекта Тьерри Брисвалтер (Thierry Briswalter) уточняет: «Еще одним фактором, безусловно, является локальная близость предприятий. Длинные маршруты транспортировки между местом производства и местом эксплуатации отсутствуют».
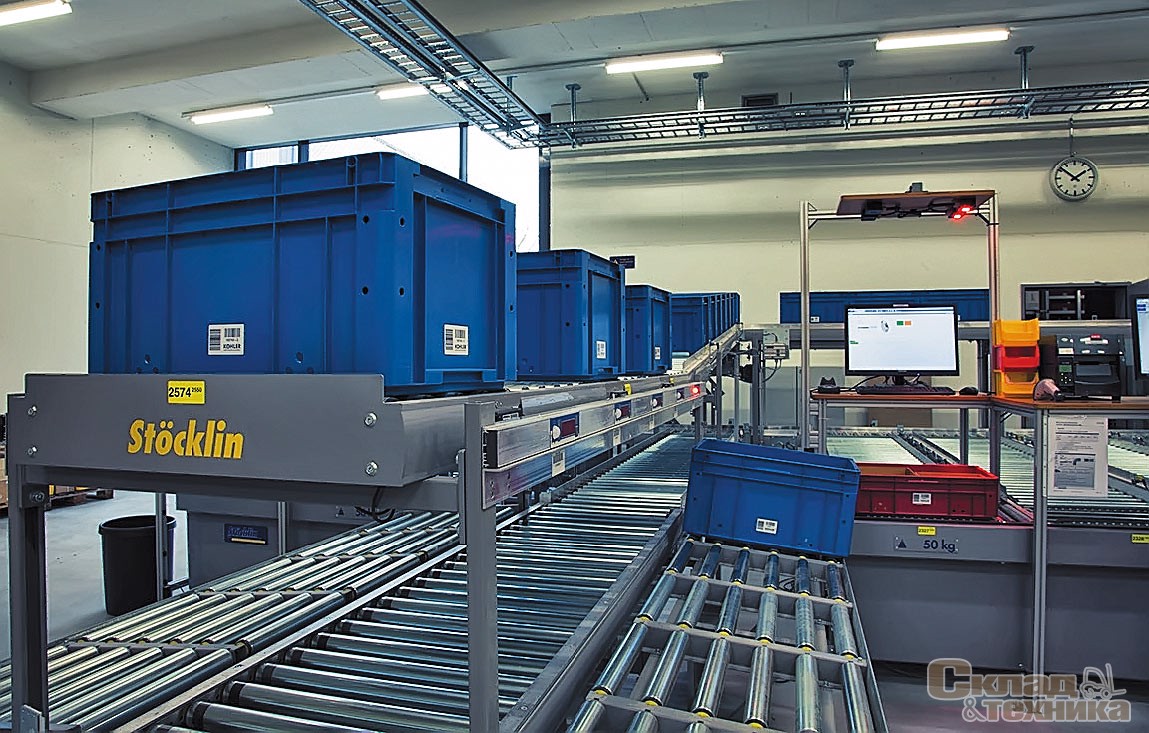
Повышенная бесперебойность и пропускная способность
Автоматизированный высотный склад (АВС) имеет длину 602 м и вмещает 6,2 тыс. мест для хранения палет (глубина хранения – одна палета). В трех проездах действуют три автоматизированные складские системы (АСС) из конструктивного ряда MASTer Stöcklin Logistik, которые могут поднимать палеты весом до 1350 кг. Одномачтовые краны, оснащенные телескопическими вилами, способны обрабатывать грузы на предписанных высотах трех проездов в 12,5; 17 и 21,5 м. На АВС применяются европалеты (евро 1, евро 2), а также палеты с размерами 1200x1200 мм. Кран-штабелер MASTer 24 имеет скорость движения до 2 м/с при ускорении 0,45 м/с2 и скорость поднимания и опускания грузов 0,50 м/с. Максимальная пропускная способность АВС оценивается в 900 палет в день.
После доставки на пункт приемки товара палеты устанавливаются на конвейеры и центрируются с помощью автоматизированного преобразователя направления, оснащенного подъемником. Одновременно посредством оптического датчика определяется их тип. С помощью расположенного с одной стороны лазерного сканера проводится идентификация палет. Здесь же находятся встроенные весы, которые служат для контроля точности комплектации через систему управления складом. После получения палеты через перевалочные пункты доставляются для размещения на хранение в АВС. На перевалочных пунктах, как и до этого на пункте приемки товара, европалеты отъезжают назад на 200 мм для того, чтобы постоянно находиться в одинаковой позиции при приеме в АВС.
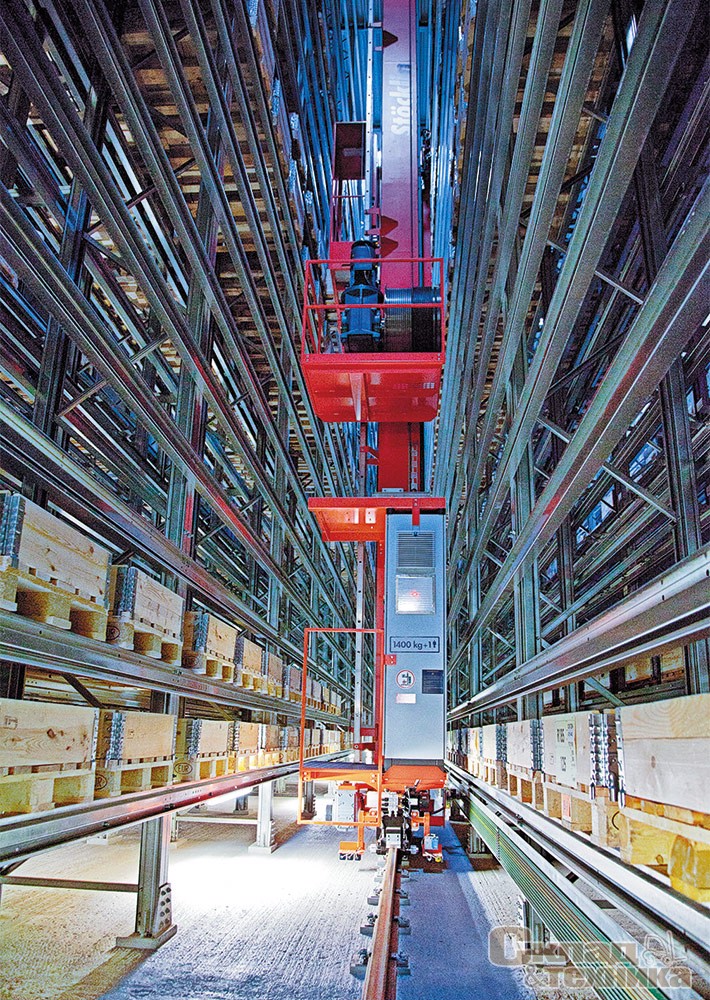
Конвейерная система, расположенная перед АВС, состоит из двух двойных станций комплектации заказа, каждая из которых имеет два конвейера, движущихся в противоположных направлениях. Затребованные для комплектации заказа палеты принимаются шаттлом и доставляются на соответствующие рабочие места, которые также оборудованы весами для проверки точности штучной комплектации заказа. Скорость движения шаттла достигает 1,0 м/с при ускорении 0,5 м/с2. «Бóльшие значения скорости теоретически возможны, но не имеют смысла из-за коротких дистанций на этом пункте», – комментирует особенности технологического процесса Брисвалтер. Как на станциях комплектации заказа, так и на пунктах перемещения и выгрузки товара, палеты регистрируются с помощью ручного сканера. Шаттл подъезжает к этим пунктам таким образом, что высота, на которой происходит комплектация изделий, является оптимальной для сотрудников. Каждый раз края палет располагаются на роликовом конвейере так, чтобы это было удобно для комплектовщика. Полную безопасность сотрудников обеспечивают четыре оптических датчика так называемой системы экстренной остановки (Mutingsystem), расположенной между станциями комплектации и шаттлом,
АСМТ обслуживается пятью кранами-штабелерами типа BOXer высотой 12,5 м, спроектированными для строений с применением облегченных конструкций. Для хранения мелкого товара в пластиковых контейнерах созданы 22 тыс. мест в пяти проездах длиной 35 м и полезной шириной 782 мм. Грузозахватное устройство представляет собой телескопический стол со стационарным ременным конвейером. С помощью крана-штабелера BOXer E1 обеспечивается передача до 2,8 тыс. пластиковых контейнеров к станциям комплектации заказа ежедневно. Таким образом, они способны выполнять до 6 тыс. перемещений в день благодаря скорости движения 4,0 м/с при ускорении 1,7 м/c . При поднимании и опускании гарантирована скорость 1,5 м/с.
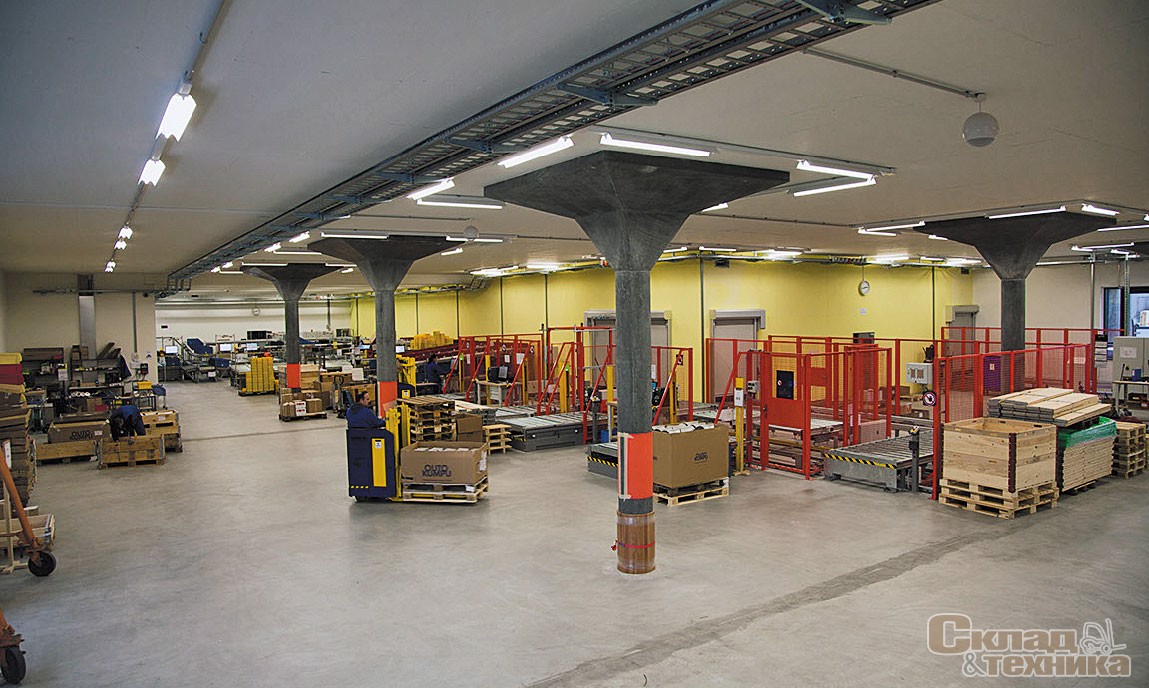
Связь с пунктами комплектации заказа осуществляется через конвейерные системы. В комплекс установки входит семь буферных линий для пластиковых контейнеров со встроенными пунктами приемки, перемещения, выгрузки и упаковки товара. В связи с ограничениями по допустимым значениям акустической эмиссии Stöcklin Logistik отказалась от применения сжатого воздуха, поэтому все механизмы являются электромеханическими. В тех местах, где должны быть перемещены контейнеры с весом до 50 кг, применяются электромеханические ременные преобразователи направления, оснащенные подъемниками.
Изъятое в процессе комплектации заказа количество контейнеров указывается с помощью технологии pick-to-light. Для обеспечения безошибочного функционирования этой технологии на каждом пункте упаковки установлен автоматизированный лазерный сканер, который идентифицирует нанесенные на контейнеры штрихкоды. Это гарантирует, что пустые пластиковые контейнеры, которые должны быть заполнены, установлены на пунктах приемки и перемещения АВС в правильном направлении. Только после того, как идентификация закончена, система управления складом указывает, как эти контейнеры должны быть поделены и заполнены. Для инициации выполнения нового заказа ручной сканер считывает штрихкод, связывая пустой пластиковый контейнер с заказом. Контейнеры, которые из-за ошибки штрихкода или неправильной высоты классифицируются как дефектные, выводятся через специальный конвейер и после устранения соответствующего дефекта снова подаются на станцию комплектации заказа. С помощью системы управления складом заказанные изделия передаются на линии выгрузки товаров. Первый пластиковый контейнер в линии идентифицируется после сканирования оператором штрихкода. На выгрузку товаров реагирует модуль индикации, после чего контейнер может быть снят. Оставшиеся на пункте выгрузки товара пустые контейнеры изымаются специальным конвейером и отправляются в буфер пустых контейнеров.
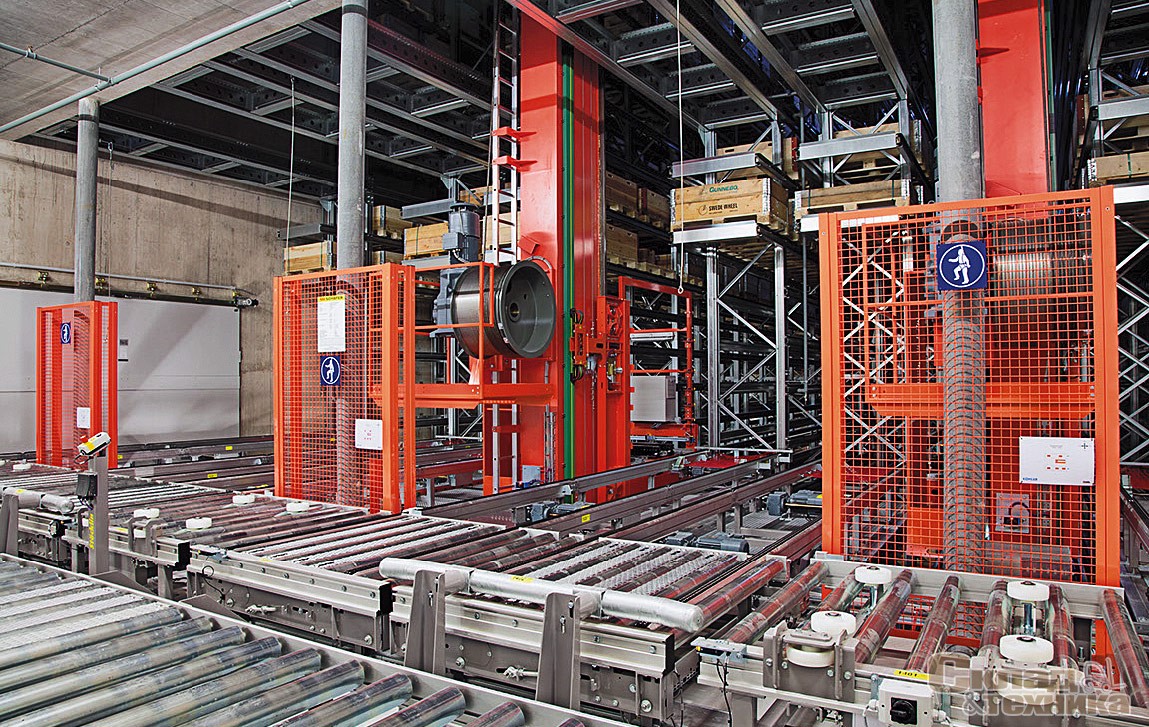
Готовность к любым случайностям
Система управления складом контролирует все заказы и логистические процессы, включая управление партиями, внутренний транспорт и погрузку. Связанный калькулятор материалопотока оснащен, помимо обычных функций, еще и системой менеджмента энергоэффективности для кранов-штабелеров. Таким образом, например, энергия торможения передается на другую ось крана через коплер шин с постоянным током. Краны-штабелеры начинают движение не все одновременно, а последовательно один за другим с коротким смещением во времени, и динамика движения зависит от размера заказа. Потребление энергии и количество рейсов кранов непрерывно измеряются и анализируются, так что есть возможность улучшенного распределения работы в зависимости от тарифов на электроэнергию. В калькулятор материалопотока встроена функция 2D-визуализации, посредством которой с пульта управления в любой момент можно получить информацию об общем состоянии работы крана в режиме реального времени. Возможные неисправности немедленно локализуются и передаются на пульт управления для того, чтоб сотрудник мог в кратчайшие сроки принять меры и восстановить бесперебойное производство. Тема визуализации уже давно стояла на повестке дня. «С помощью моделирования всего оборудования в часы пик сначала сверяется схема и расчет параметров», – поясняет Тьерри Брисвалтер.
Бенно Кюниг удовлетворен этим реализованным решением: «Нам удалось обеспечить максимальную производительность на сравнительно небольшой площади и одновременно увеличить вместительность склада, включая резервы». Это были основные цели проекта GIZELA, инициированного АО Hans Kohler.